
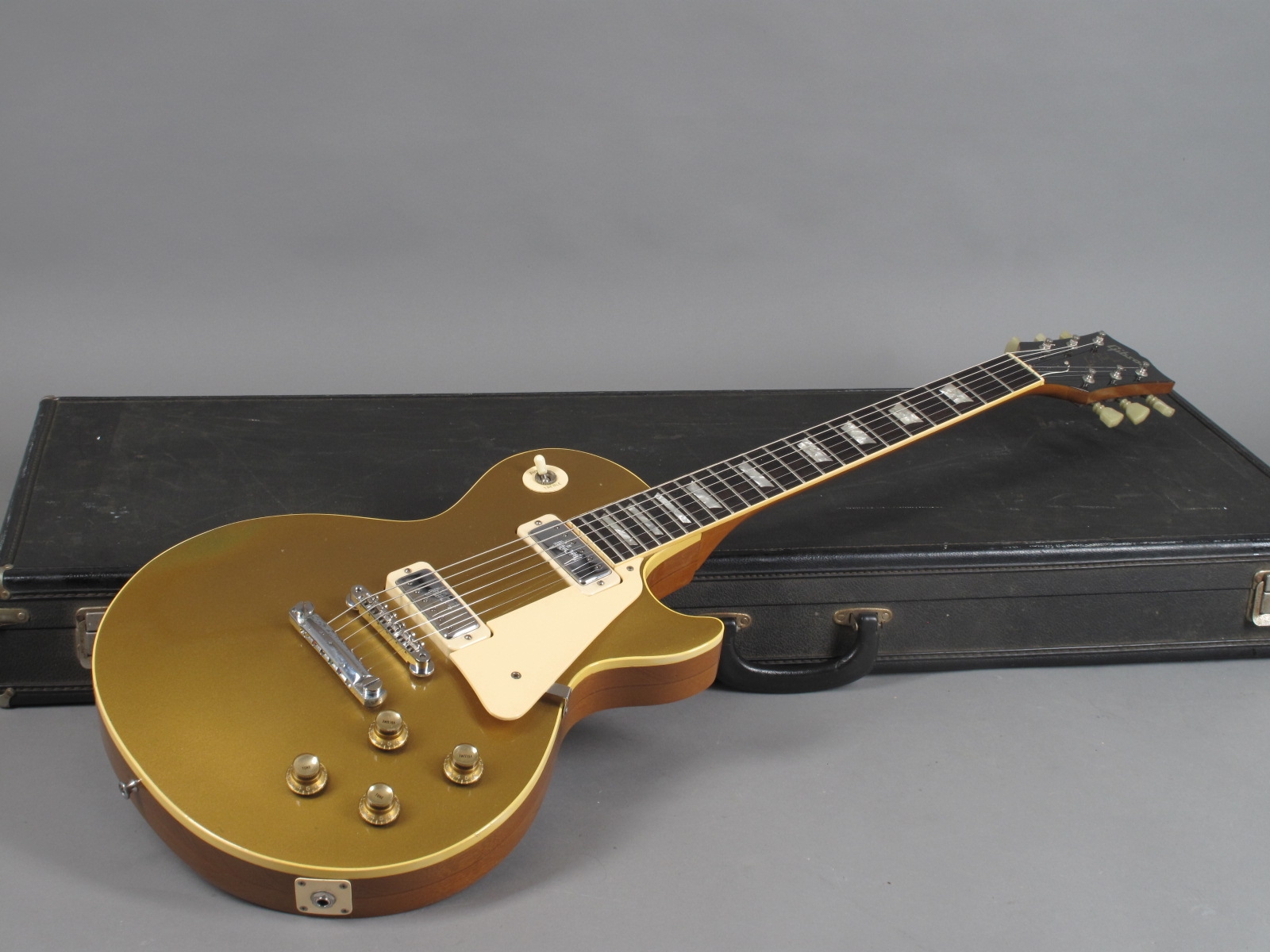
According to Edwin Wilson, the Gibson Custom Shop’s Historic program manager, lacquer from different eras checked in various ways depending on the formulation.

Needless to say, inducing lacquer checking is a fundamental part of the faux-ageing process. It’s caused by rapid fluctuations in temperature, and over the years can develop into intricate and fascinating patterns that many people find aesthetically pleasing. Checking OutĪlmost every vintage guitar with a nitrocellulose finish will show some degree of lacquer checking. Fortunately, however, things start to improve from this point onwards. I don’t particularly enjoy this part of the process because at the end of it the body looks worse – more like a nice finish that has been subjected to random acts of violence. You can flake them out and modify the shape and size of the dent using one of these dental tools Loose bits of chipped lacquer never look quite right. To achieve the jagged edges, I flake away the finish using my fingernails, taking care to avoid scratching or denting the wood.

It’s actually quite a slow and gentle process that doesn’t require specialist ‘tools’ such as bicycle chains or belt sanders. To simulate the effect, I rub through the finish with slightly damp 1000 grit wet and dry paper, followed by finer grades of micromesh. In my experience, vintage edges tend to be more jagged and rough. It’s a nice effect, but it’s rare to see genuine vintage guitars with that sort of wear – and the sanding lines can be a giveaway. When that’s done, you get to see the layers of tinted topcoats, colour and base coats and the wood beneath. I’m partial to a bit of rub-through on the upper bout, but many artificually-aged instruments are merely sanded in this area. Here, the lacquer has been chipped through to expose the wood In the natural ageing process, guitar bodies usually get chipped around the bottom edges. Look for pictures of genuine vintage guitars with the same body shape as you are working on and you will be able to identify the areas that tend to take the brunt of things and copy the wear patterns.

You can go for larger chips around the edges, and I sometimes use a dental tool to flake off the lacquer. Achieving a convincing look requires variety and randomisation. I also try to tap the finish strategically with blunt objects and screwdriver shafts. The bridge, pickguard and control plate also ensure dings and dents end up in the right places Having them in situ provides a modicum of protection in the surrounding areas and will give you more realistic results.Īll the fixtures and fittings have to go onto the body to ensure they line up properly. Adding too many chips and deep dents can look a bit over the top.īefore dinging up the finish, I fit the string ferrules, pickguard, bridge, neck plate and control plate because it’s unrealistic to damage the finish under those areas. It’s actually quite hard to gauge because dents that are seemingly superficial can look far more prominent later on. This is why you have to damage the paintwork before cracking the lacquer Notice how the lacquer checking lines correspond with the dings and dents. Remember to do the sides as well as the front and back – and be aware that the longer the drop, the deeper the dents. Like the guys at Fender and Gibson, I collect several bunches of keys and simply drop them onto the body. Look closely at genuine vintage finishes and you’ll see that’s how things tend to happen in the ‘natural world’, and it can look amazing. My approach is to begin by adding dings, dents and chips to the finish because when I get the lacquer to check later, the lines will form around these marks. This is the point of no return because it’s the last time this beautiful nitro finish will ever look like new This will be your final opportunity to ask yourself if you really want to go through with the process, because there’s no going back. The RelicĪt the start of this process, you may well find yourself staring at a shiny and pristine finish. When this guitar is finally assembled, both the neck and bridge will be coupled directly to the body. After removing the tape, I sanded away the overspray with a small block. I followed the same procedure for the neck pocket, cutting the masking tape just inside the outer edges of the neck pocket. Here, it has been used to remove sprayover from the edge of the neck pocket You can make a mini sanding block from a small offcut of hardwood and double-sided tape. I peeled the tape from the outside in to reduce the risk of causing damage to the finish. To remove the tape, I scored around the edges with a craft knife then cut across the middle of the pickup rout. The tape had to be left in situ until the finish had cured properly and the cutting and polishing process had been completed.
